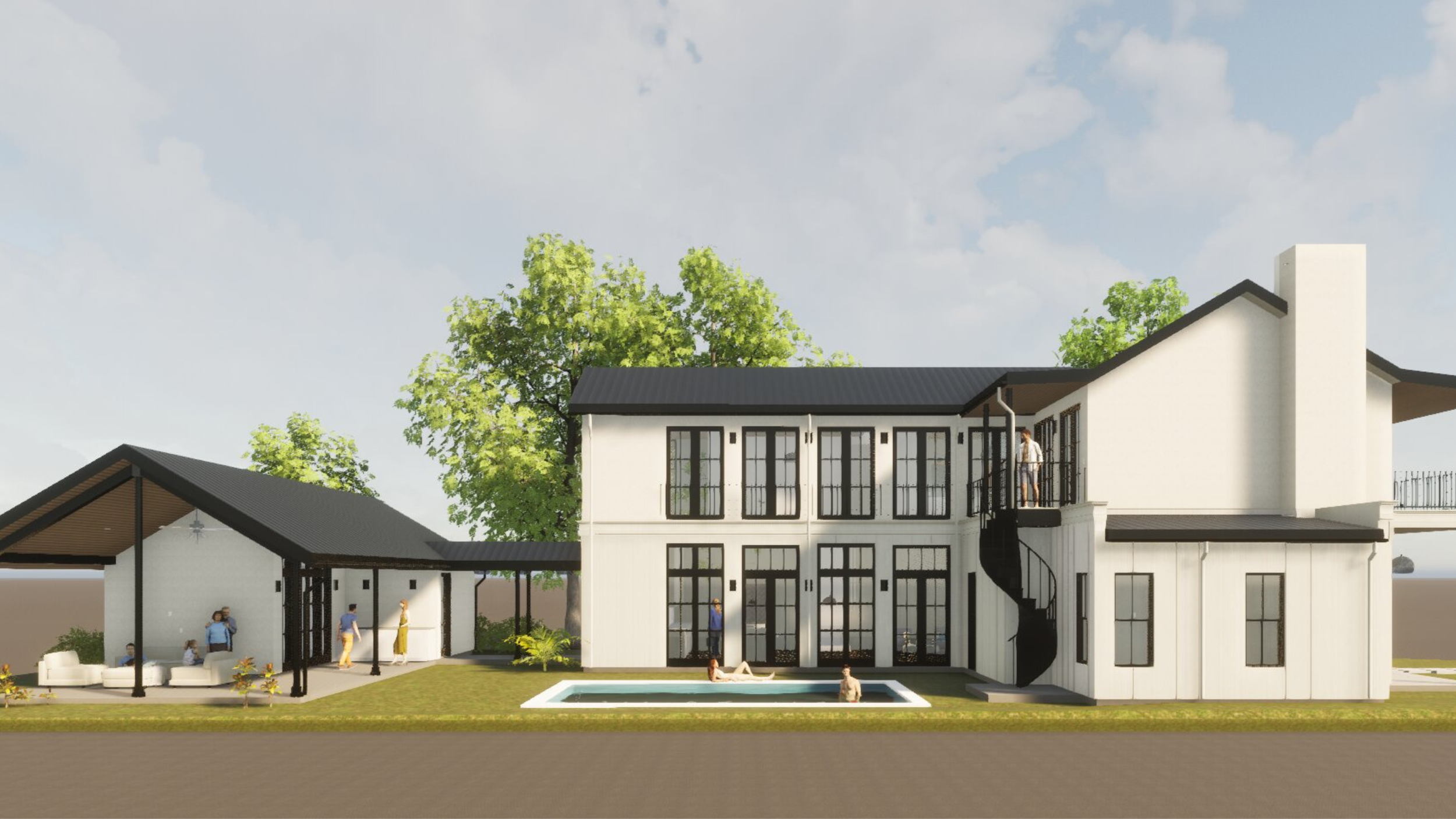
Take a few minutes and watch the videos below to learn what makes us stand apart.
The Power of Colloboration
Working with a design build firm offers a unique value add in the custom building industry. Unlike the traditional approach where various professionals work in isolation, a design build firm brings together architects, interior designers, lighting designers, structural engineers, and other experts to collaborate and communicate effectively. By fostering a cohesive and integrated team, they ensure everyone is aligned and working towards the same goals. This streamlined approach leads to a seamless and enjoyable home building experience for clients, resulting in outstanding results. So, if you're looking for a hassle-free and successful project, working with a design build firm is the way to go. Adios, amigos!
If you’re not testing, you’re guessing!
We ended up approximately 10 times better than what code requires, & I’m confident we can achieve even lower blower door (air leakage) scores on our future homes.
How We Build Tight Houses
With almost 19 years of experience as a builder, I've come to appreciate the importance of maintaining points of control throughout a project. While consulting on a project, I noticed some differences in how others approach construction.
For instance, the soffits, roof underlayment, and windows and doors were installed at different stages. If it were my project, I would have preferred to have all the windows, doors, and MEP (mechanical, electrical, plumbing) installations completed first. By doing so, I can ensure that the building is fully dried in and undergoes a thorough blower door test for air tightness. This allows me to address any deficiencies and make adjustments before moving forward. If the soffit and roof underlayment were already in place, it would limit my ability to control and rectify any issues discovered during testing. Maintaining this level of control and precision throughout the construction process is how we approach building.
Inside the Walls: Mastering MEP Installation
In this video, Doug details the MEP sequence for framing houses. We begin by installing HVAC systems due to their large duct requirements, followed by plumbing for drain and water lines, while electricians set up outlet and fixture boxes. Each step is coordinated to ensure precise alignment of systems. The final stages include electrical wiring and low voltage installations. This thorough process typically spans one to two months, emphasizing careful planning and execution to ensure everything fits perfectly within the construction plan.
Leading Sustainability: How Our Unique Use of Insulated Zip-R Panels Revolutionizes Home Building
We are still the only builder in the country, that I’m aware of, using insulated Zip-R panels on our roofs (R stands for thermal Resistance), in addition to our walls. This innovative off-label practice provides our buildings a continuous thermal break, meaning our homes experience almost zero thermal bridging (regardless of how hot or cold it is outside, & without any chemical laden spray-foam). No thermal bridges = no chance of “dew point” occurring in our wall or roof cavities, greatly reducing opportunities for mold to grow & increasing the chances of our homes lasting for centuries (yes centuries) & being multi-generational & holding historic designations. This practice definitely reduces electric bills too while simultaneously maximizing occupant comfort (no drafts or heat islands). #BuildingScience fundamentals lead us down this path & we are not looking back….#Sustainability is sexy!